The process of die casting
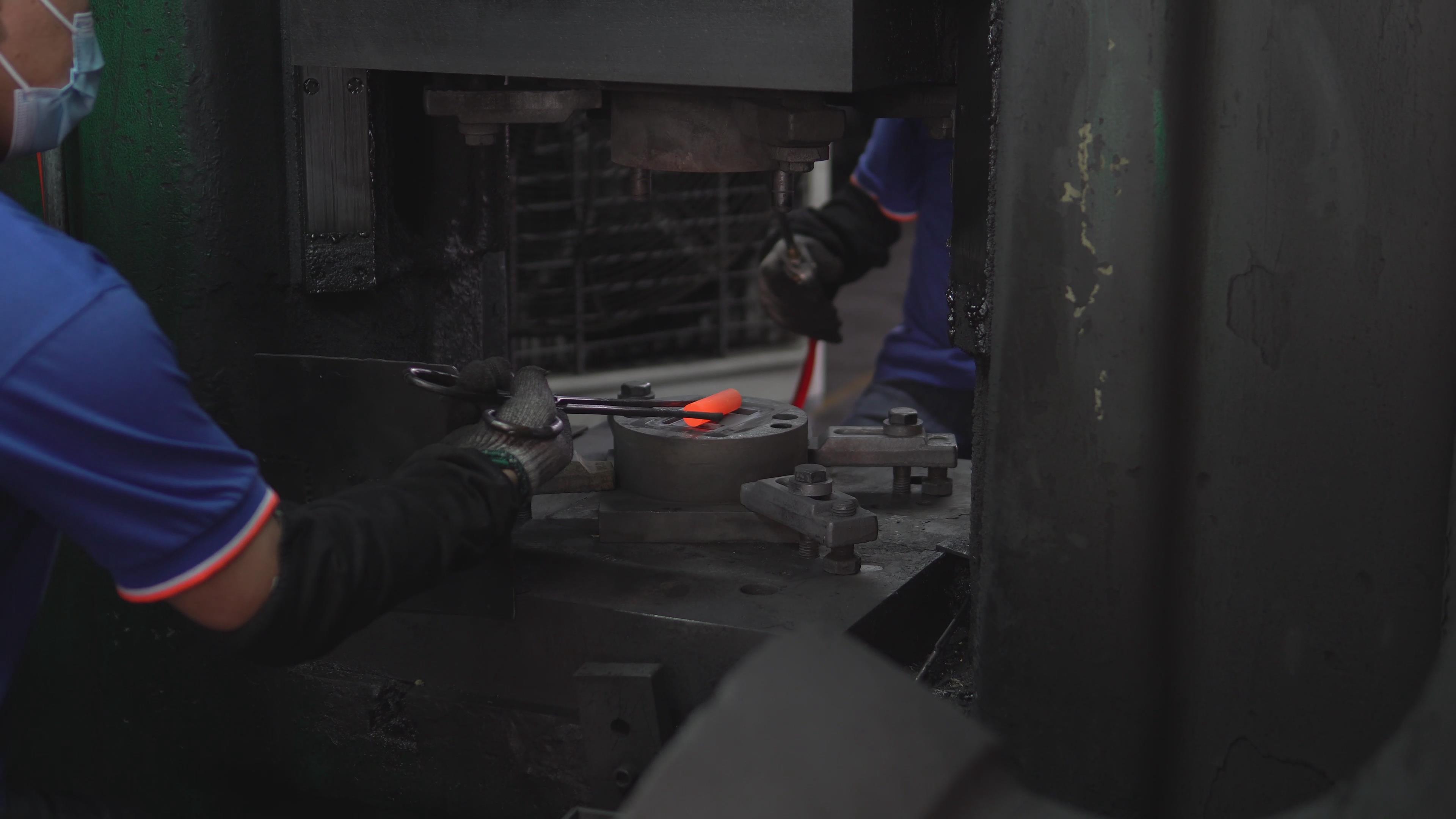
Die casting is a process that involves melting low melting point metals (such as copper and aluminium) and injecting them into an already made mould called a die casting die. The process of die casting is efficient and economical, offering a wide range of shapes and components. The components produced have a long service life. The advantage of this production process is that hundreds of thousands of castings can be produced relatively quickly using only one mould. All parts produced are of uniform quality and the unit costs involved are relatively low. But how does the manufacturing process actually work?
The standard process for both hot chamber and cold chamber die casting is to inject molten metal into the die under high pressure. The following are the steps of the complex die casting process.
- Clamping
The first step in die casting is clamping. Before this, however, the mould is cleaned to remove any impurities and lubricated for better injection and removal of the cured product. After cleaning and lubrication, the moulds are clamped and closed with high pressure.
- Injecting
Melt the metal you want to inject and pour it into the injection chamber. This process depends on the process you are using. In cold chamber die casting, for example, the injection chamber is cold, whereas in hot chamber die casting it is hot. Afterwards, the metal is injected into the mould under the high pressure generated by the hydraulic system.
- Cooling
While clamping, the metal is allowed to cool and solidify. The solidified material will have a shape similar to that of the mould design.
- Ejecting
After releasing the mould, the eject mechanism pushes the solid casting out of the mould. Proper solidification is ensured before the final product is ejected.
- Trimming
This is the final step and involves removing excess metal from the gates and runners found on the finished product. Trimming can be achieved by trimming the mould, a saw or other procedures. The metal parts removed during this process are recyclable and reusable.
The die-casting process is of great importance in the production and manufacture of shower hardware. In response to what you have read, please add your comments below for more information.